Sometimes mistakenly called pressure-treated lumber, PT lumber is an abbreviation for “preservative-treated” - Wood preservatives help protect lumber from attack by insects and decay, but there are a few important things to understand about it before using it as a building material.
The Basics
What is PT lumber?
“PT” lumber is an abbreviation for “preservative-treated” lumber. While sometimes called “pressure-treated” lumber, only some types of preservative treatment are applied to wood under pressure. Wood preservatives help protect lumber from attack by insects and decay. There are types of lumber that are naturally decay resistant and do not require preservative treatment when exposed to weather – like western red cedar, redwood, and others. These types of wood are generally much more expensive than treated lumber, and also generally have lesser structural design values. Therefore, PT lumber is a “go-to” building product for exposed exterior framing.
What is the lifespan of PT lumber?
The expected useful life of exposed PT wood depends on many factors including environmental conditions and wood preservative type. According to Fannie Mae (Form 4099.F – August 2019), the estimated useful life of residential “wood decks” is 20 years, and “exterior wood stairs” is 15 years. The Western Wood Preservers Institute (WWPI) estimates 25+ years for properly designed and preservative treated wood.
Not all PT lumber is created equal
There are many levels of treatment depending on the type of wood and what it will be exposed to. Solely specifying lumber to be “preservative treated” is ambiguous. The American Wood Preservative Association (AWPA), which is what building codes refer to for PT wood requirements, has 5 levels of “Use Categories” not including sub-categories.
-
-
- UC1 is for interior protection against insects
- UC2 is for interior damp conditions which includes mudsills bolted to concrete foundations
- UC3A is for exterior protected areas including wood well covered by a roof
- UC3B is for exterior exposed conditions including deck and stair stringers
- UC4 categories are for different levels of ground contact
- UC5 categories are for various marine exposures
Different types and amounts of chemicals can be used to achieve different Use Categories. The lower the Use Category, the less the amount of preservative is present in the wood and the less resistant it is to insects and decay.
Field treating PT lumber
Wood preservative coats the outside surface of the wood and it penetrates/absorbs to the interior of the wood member only to a degree, depending on treatment method. The center of a piece of PT wood typically does not contain wood preservative. This is apparent when you observe a freshly cut piece of PT lumber: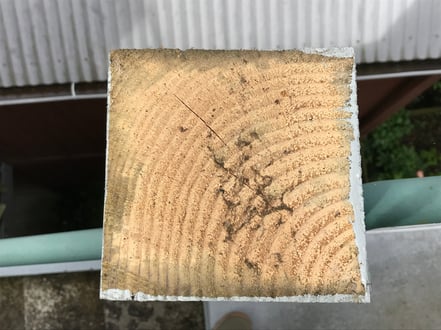
Code requires “all cuts, holes, and injuries such as abrasions or removal of nails and spikes or other damage to the treated zone to be field treated with an approved preservative.” This takes care, on the contractor’s part, to perform this tedious work in addition to the challenges of framing.
Evaluating PT Lumber - Visual indications
The following are items to look for when inspecting PT lumber framing:
1. Is the lumber incised?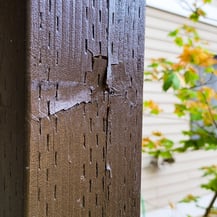
The typical framing lumber species in the northwest are Douglas Fir, Larch and Hemlock (which are typically classified as Doug Fir-Larch or Hem-Fir). In order for these species to be able to absorb enough preservative treatment to meet a Use Category of UC3B (typical exposed deck framing), there must be little cuts, or incisions, made in the wood to increase the penetration of the treatment. If you don’t see incisions, the exposed lumber is probably not properly preservative treated.
2. Are notches, holes and other damages field treated? Look for discoloration (and a yummy smell) of topical treatment at notches and holes. These are often locations where decay will start if not field treated.
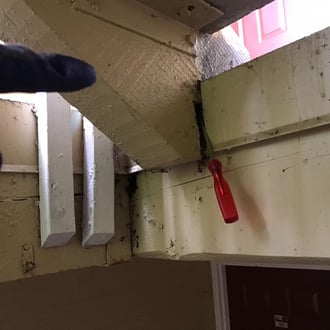
3. Are “beams” in contact with the ground?
Incised square “posts” (4x4’s, 6x6’s, etc.) are often treated to UC4 standards for ground contact. However, incised rectangular “beams” (4x8’s, 4x10’s, 2x8’s, etc.) are typically treated to UC3 standards—not for ground contact. Despite this, the latter is the type of lumber that is typically used for stair stringers, which often sit on the ground. Look for decay to start at these locations. 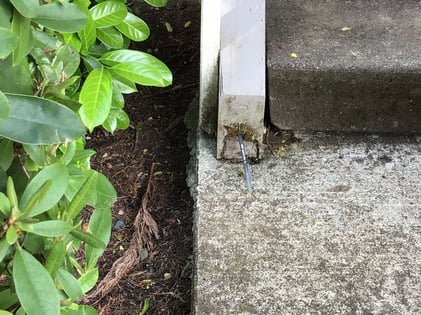
4. Is lumber treated to the proper Use Category?
Verify that the lumber use is appropriate for the exposure. There are some preservatives that leach out when exposed to water, and you don’t want to use this lumber for an exposed deck. 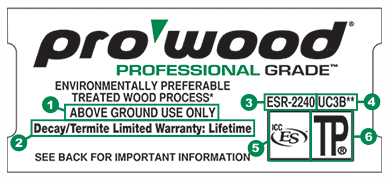
Image source: Hillside Lumber
Testing methods
Since the treatment is only on the outside surface of the framing, it’s not always obvious if PT lumber is decayed at the center. The following methods can be used to help determine the overall condition:
Hammer test
“Knock” on the wood with a hammer. If it sounds hollow, it probably is.
Pick test
Stick a screwdriver into the wood with the flat tip parallel with the grain. Then, pry. If the wood splinters, it might be fine. If it breaks directly above the screwdriver tip, it is likely decayed (even though it “feels” hard).
Resistance drilling
These are tools that are used to check trees for decay. They also help with building inspections by measuring the force it takes to drill through wood. The downside is they only check at the exact ¼” where the drill bit travels, and wood is extremely non-uniform.
Stress wave testing
These are tools that measure how fast soundwaves travel through wood. Results are greatly affected by wood decay.
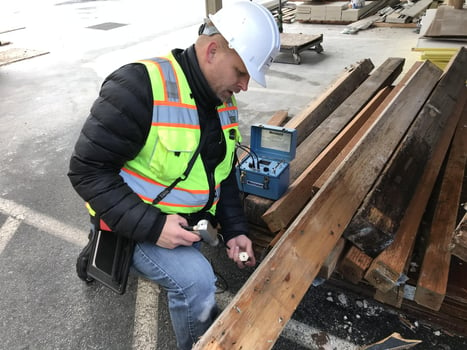
Invasive Observations
If in doubt, cut the wood in half and check out the center.